|
Medium Complex Large Metal Parts
by Wire Additive Manufacturing |
 |
|
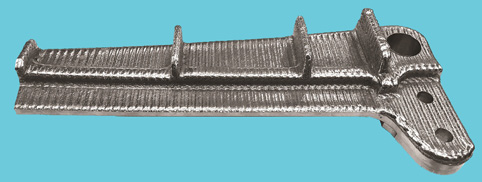 |
☆ Truss work Part on Plane |
☆ Titanium wires for 3D Printing |
1. Wire AM vs. Powder Bed AM
Wire AM is a very promising technology for producing large components with moderate complexity, such as stiffened beam. Its strengths and weaknesses comparing with powder bed AM are shown as follows:
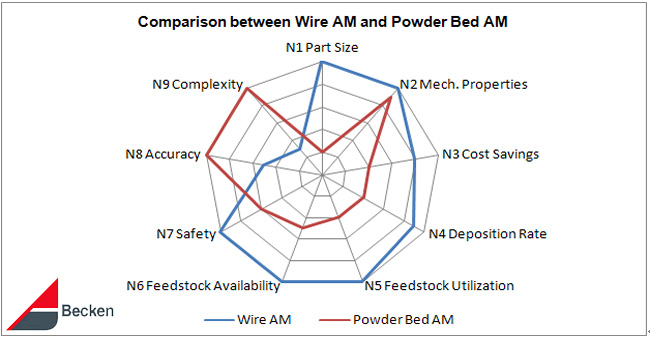 |
N1: Powder BED AM technology can only produce parts of very limited sizes. Becken Metal parts manufactured by Wire AM can reach the size of 6-10 meters long, this enables us to cooperate with industries like aircraft, aerospace, oil and gas etc. |
|
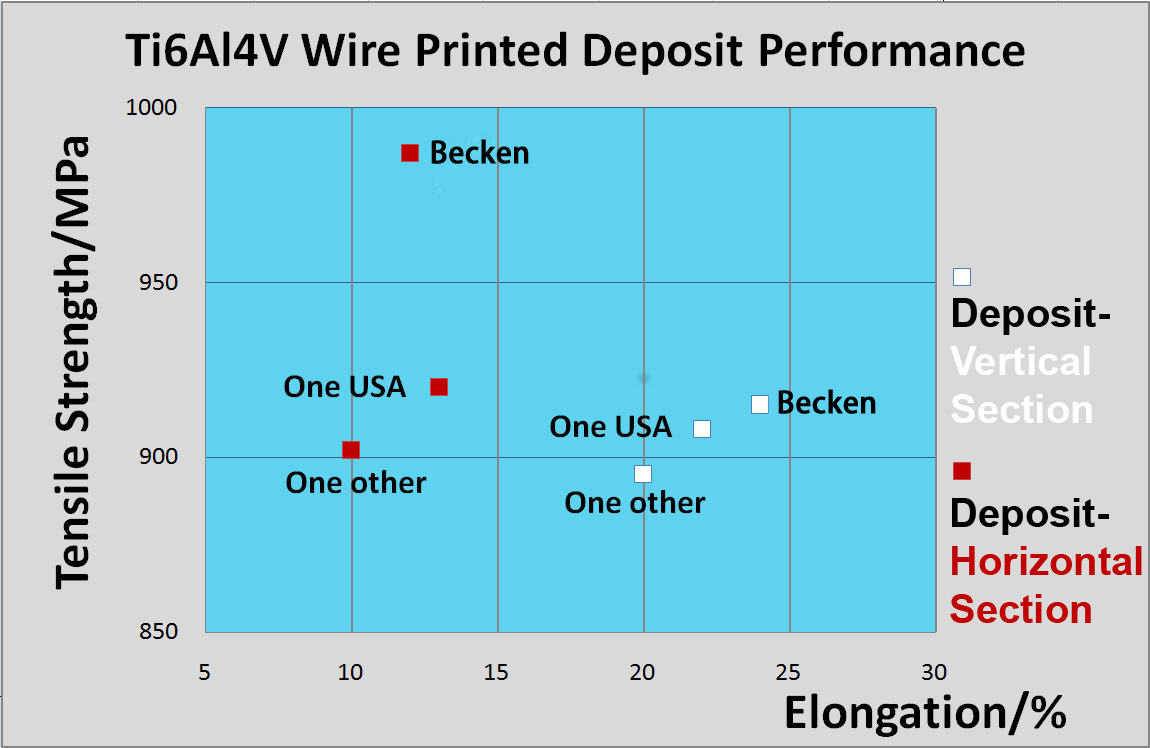 |
|
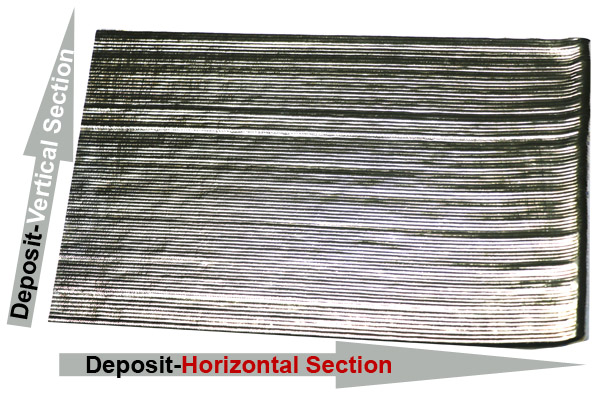 |
N2: The mechanical properties by Wire AM are better than those by powder bed AM due to its 100% dense structure. Besides, with our top perofrmance wires, we Becken, long-term member of the International Titanium Association, guarantee that our parts will be first-class substitutes for those by cast and wrought.
N3: Powder feedstock is much more expensive than wire feedstock across the board.
N4, N5: Wire AM has a much higher material feedstock utilizaition rate up to 100 % and deposition rate
2-4 times than powder bed AM.
N6: Wire AM will provide the users with a wider range and greater availability of feedstock, more various types of Titanium or Nickel alloys etc.
N8, N9: Powder bed AM has a much higher accuracy and complexity than wire AM.
|
2. Application
|
- Aircraft frames, structures, and parts
- Aerospace
- Oil & Gas Equipment
- Industrial Pump Components
- Nuclear Power Components
- Industrial Mould
|
|
|
 |
 |
|